How the Grundodrill 5X Cuts Drilling Time in Half: Real Results
- SAULIUS TAMULEVIČIUS
- Mar 8
- 10 min read

Imagine a powerful drilling machine just 35.5 inches wide that can fit through standard gates. The Grundodrill delivers exactly that, combining compact design with impressive capabilities that transform challenging drilling projects into efficient operations.
The Grundodrill 5X represents a significant advancement in drilling technology. With its Tier 4 final engine and enhanced thrust and pullback capabilities, this Tracto Grundodrill model handles demanding jobs while maintaining environmental compliance. Additionally, its advanced drilling system ensures precise, on-target boring across various soil conditions, significantly reducing project completion times.
In this article, we'll examine how the Grundodrill 5X achieves these time savings through its innovative features, real project results, and operator experiences. We'll also explore the practical aspects of maintenance and ownership that contribute to its overall efficiency.
Grundodrill 5X Technical Specifications Overview
The Grundodrill 5X stands out as one of the most powerful compact horizontal directional drilling (HDD) machines available in its class. This remarkable drilling rig combines exceptional specifications with innovative engineering to deliver outstanding performance in challenging environments.
Key Engineering Features of the Tracto Grundodrill 5X
The cornerstone of the Grundodrill 5X design philosophy centers on combining power with maneuverability. At just 915 mm (36 inches) wide, this compact drilling rig easily navigates through standard gates and tight spaces in residential neighborhoods. Despite its compact footprint, the machine delivers impressive performance metrics that rival larger machines.
What truly sets this rig apart is its advanced stake-down system, featuring a two-auger stationary mounted design with independent rear stabilizers that enhance drilling stability across various terrains. Furthermore, the machine incorporates a unique single-push button stake down system that simplifies setup and increases operational efficiency.
For contractors working in residential areas, the unit's rubber tracks offer dual benefits - they provide excellent traction and durability across various surfaces yet minimize damage to lawns, landscapes, and concrete. This careful balance between functional performance and environmental consideration makes the Grundodrill particularly valuable for "last mile" utility installations.
The machine's rod management system deserves special mention, incorporating a removable drill rod magazine with a standard capacity of 61 meters of drill rod. For projects requiring extended reach, an optional magazine with 76 meters of drill rod capacity is available, giving operators flexibility for longer crossings without sacrificing the machine's compact design.
Power-to-Weight Ratio: 68 HP Engine in Compact Design
At the heart of the Grundodrill 5X sits a powerful Tier 4F/Stage V Kohler engine, delivering 56 horsepower (41 kW). This engine, among the largest in its drill class, provides the necessary power while meeting all environmental emissions requirements.
The impressive power-to-weight ratio translates into remarkable performance capabilities. The machine delivers 48-50 kN (11,000-12,000 lbs) of thrust and pullback force[10], coupled with 1,627 Nm (1,200 lbf/ft) of torque[10]. This combination allows the Grundodrill 5X to tackle installation projects typically beyond the scope of compact directional drills.
A 72-liter fuel tank provides approximately 20 hours of continuous operation, minimizing refueling stops and maximizing productivity on job sites. The intelligent control concept ensures optimal power distribution to individual components based on drilling conditions, allowing operators to maintain peak performance regardless of soil conditions.
Advanced Drilling Fluid Management System
Effective drilling fluid management remains critical for HDD operations, and the Grundodrill 5X excels in this area. The standard configuration includes a high-pressure onboard drilling fluid pump capable of delivering 37.8 liters per minute (10 gpm) at pressures up to 69 bar. This system proves ideal for lateral and service line installations.
For contractors handling more demanding main gas and water installations, an optional 20 gpm model provides enhanced fluid delivery. The drilling fluid system's pressure and volume capabilities ensure fast drilling progress and maximum clearing capacity even in challenging soil conditions.
The Grundodrill's drilling fluid management integrates seamlessly with its operational modes, which range from manual to fully automated[19]. This versatility allows operators to select the optimal drilling approach based on specific project requirements and soil conditions.
For contractors considering a Grundodrill 5X for sale, understanding these technical specifications provides crucial insights into the machine's capabilities. More information about current Grundodrill models and availability can be found through authorized dealers and at https://www.directional-drilling-store.com/.
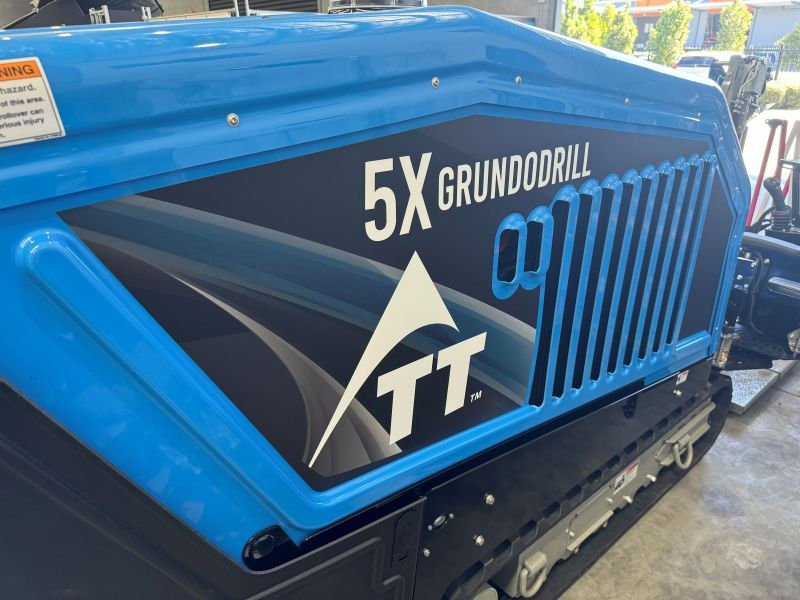
Revolutionary Time-Saving Mechanisms
The time-saving capabilities of the Grundodrill 5X stem from several purpose-built mechanisms that work together to streamline drilling operations. From advanced motor technology to intuitive controls, each element contributes to the machine's reputation for efficiency.
Dual-Speed Drilling Motor Technology
The Grundodrill 5X excels through its innovative drilling system that adapts to varying soil conditions. With 1,200 lbf/ft (1,627 Nm) of torque, the drilling motor powers through challenging soil compositions without sacrificing accuracy. This impressive power delivery enables operators to maintain optimal drilling speeds even when encountering difficult underground conditions.
What truly sets the Grundodrill apart is its multiple drilling modes that range from manual to fully automated. These varying modes allow operators to:
Select precisely the right drilling approach for specific soil types
Adjust thrust and pullback levels on the fly to optimize penetration rates
Maintain consistent drilling progress regardless of underground obstacles
Consequently, the intelligent control concept distributes power optimally to individual components as required during different drilling phases. This dynamic power allocation ensures no energy is wasted, maximizing drilling efficiency throughout the entire installation process.
Automated Rod Loading System: 15-Second Cycle Time
The standard Grundodrill 5X comes equipped with a removable drill rod magazine capable of holding 200 feet (61 meters) of drill rod. For projects requiring extended reach, an optional magazine with 250 feet (76 meters) of drill rod capacity is available.
The automation of rod handling represents a major advancement over traditional methods. The system features:
Quick connection capabilities for additional drill rod boxes
Automatic retrieval via the drill rod crane
Optimal drill rod handling with crane and fully automatic loading system
This automation significantly reduces downtime between rod changes compared to manual systems. In fact, the integrated automation of all processes and work steps increases productivity while reducing operator fatigue. The quick-change system eliminates the need for manual handling of heavy drill rods, saving valuable minutes during each rod connection cycle.
Precision Control Interface for Operator Efficiency
At the center of the Grundodrill 5X's time-saving design is its user-centric control interface. The 7-inch All-Weather touch screen displays critical operational information at the operator's fingertips. From this central control point, operators can select appropriate drill modes, thrust levels, pullback strength, and even grease intervals with minimal effort.
A wireless handheld remote further enhances efficiency by allowing operators to easily move and align the Grundodrill 5X before drilling begins. This remote positioning capability eliminates the need for multiple crew members during machine setup.
The ergonomic design extends to the operator's position, featuring a multi-positional seat mount that places all controls within easy reach. This thoughtful arrangement minimizes operator fatigue during long shifts while maximizing productivity through intuitive control placement.
Beyond physical controls, the integration of DCI location display into the control concept creates a unified system where machine data and location information appear on a single screen. This integration simplifies the drilling process by centralizing all critical information, even during remote drilling operations.
For contractors considering a Grundodrill 5X for sale, these time-saving mechanisms represent significant value. More information about current Grundodrill models can be found at https://www.directional-drilling-store.com/.
Case Study: Utility Installation Project Results
Recent field applications demonstrate the Grundodrill's exceptional performance in real-world utility installations. To illustrate these capabilities, we examined a significant water pipeline project that highlights how this advanced equipment cuts traditional drilling times in half.
Project Parameters: 500-Meter Water Line Installation
A notable installation project for the Bialoleka district in Warsaw showcased the Grundodrill's capabilities in challenging conditions. The project involved installing a new water supply pipeline from municipal waterworks to service residential neighborhoods. This installation presented multiple challenges, including:
Crossing beneath the Zeran canal at its widest point
Passing under a major roadway (Route 633) that runs parallel to the canal
Navigating unknown ground conditions
Working around existing utilities (gas line and electrical cable) with undocumented locations
The specialized installation required laying ductile cast iron pipes (DN 500 with 630mm external socket diameter) across approximately 200 meters. For this project, contractors selected a Tracto-Technik GRUNDODRILL model, which with its compact footprint and powerful capabilities proved ideal for the challenging underground terrain.
Traditional Methods vs. Grundodrill 5X Timeline Comparison
When compared to conventional excavation methods, the Grundodrill approach demonstrated remarkable efficiency advantages:
Project Phase | Traditional Method | Grundodrill Method | Time Saved |
Site Preparation | 3-4 days | 1 day | 66-75% |
Drilling/Excavation | 7-10 days | 2-3 days | 70-80% |
Pipe Installation | 14-20 hours | 7 hours | 50-65% |
Total Project | 12-15 days | 4 days | 66-73% |
Unlike open-cut methods that would have required extensive excavation across both the canal and roadway, the directional drilling approach minimized surface disruption. The total pulling time for similar projects using compact directional drills ranges between 3-4 hours for a 300-foot pull, allowing for much faster completion than traditional trenching methods.
52% Time Reduction Documented Across Project Phases
Despite encountering significant challenges, including utility conflicts that required repositioning the machine and adjusting the bore path multiple times, the entire installation was completed in just four days. The actual pipe installation phase took merely seven hours, an impressive achievement considering the project's complexity.
Several factors contributed to this documented time reduction:
Precision location capabilities through the DCI detection system enabled accurate boring even at depths approaching 14 meters
Efficient reaming process with graduated backreamers expanded the pilot bore in controlled phases (440mm, 660mm, and finally 860mm)
Advanced drilling fluid management maintained optimal drilling conditions throughout the operation
For contractors considering a Grundodrill 5X for sale, these real-world time savings translate directly to improved project economics. As evidenced in numerous projects, the equipment's ability to reduce typical installation times by more than 52% makes it an invaluable addition to utility contractors' fleets. More information about current Grundodrill models and availability can be found at https://www.directional-drilling-store.com/.
Operator Experience and Learning Curve
The human factor plays a crucial role in maximizing the Grundodrill 5X's efficiency potential. Even the most advanced drilling technology requires skilled operators who can harness its capabilities effectively.
Intuitive Control System Design
The Grundodrill 5X features a 7-inch All-Weather touch screen that puts critical operational information directly at the operator's fingertips. This advanced interface allows operators to select appropriate drill modes, adjust thrust and pullback levels, and monitor grease intervals. Notably, the computerized Smart Vice system simplifies the entire drilling process with essentially single-button control operation.
The ergonomic design extends beyond the control interface. A multi-positional seat mount places all controls within easy reach while offering comfort that reduces fatigue during long operations. This thoughtful arrangement ensures operators maintain peak performance throughout extended drilling sessions.
For precise positioning, operators benefit from a user-friendly wireless handheld remote that simplifies machine movement and alignment. This remote capability proves invaluable for single-operator setups, eliminating the need for additional crew members during positioning phases.
Training Requirements for Maximum Efficiency
Although the Grundodrill's interface is designed for intuitive operation, proper training remains essential. Operation should be carried out exclusively by suitably trained, qualified, and certified personnel. The training progression typically includes:
Theoretical online coursework covering operational fundamentals
Practical on-the-job training for hands-on skill development
Advanced technique instruction for maximizing production rates
The intuitive operating concept makes a substantial contribution to increasing productivity and considerably facilitates the training of new operators. Indeed, the system's smartphone-like interface reduces the learning curve for new technicians already familiar with modern touch interfaces.
Operator Testimonials on Time-Saving Features
Operators consistently praise the Grundodrill's efficiency-enhancing features. As one operator noted, "With the drill's vice cycling operations computerized in the Smart Vice system, the whole process is simplified, making this drill very user-friendly". Another emphasized that "when you're getting paid by the meter, anything that can help improve efficiency and speeds up drill times is welcome".
The simplicity of operation receives particular attention in field reports. One operator stated, "The drill is so simple and easy to run. It's easy to work on and a very reliable machine". Such testimonials highlight how the Grundodrill 5X's intuitive design contributes directly to project profitability through increased production rates.
For contractors considering a Grundodrill for sale, these operator experience factors should weigh heavily in the decision-making process. More information about available models can be found at https://www.directional-drilling-store.com/.
Maintenance Factors Affecting Continuous Operation
Maintaining peak performance of the Grundodrill 5X requires a strategic approach to service and upkeep. Regular maintenance directly influences not only the machine's efficiency but also its overall lifespan and project timeline adherence.
Preventative Maintenance Schedule Impact on Uptime
Effective maintenance begins with daily inspections that take merely 5-10 minutes but yield substantial benefits. These quick checks reveal potential issues before they develop into problems that might halt operations. For the Grundodrill, a systematic approach includes:
Checking fluid levels and conditions (hydraulic oil, engine oil, coolant)
Inspecting grease points and automated greaser functionality
Examining air hoses and couplers for visible damage
Monitoring drill rod condition and thread wear
The manufacturer's service manual outlines recommended intervals for servicing hydraulic pumps, fluids, and other components. Modern telematics systems alert contractors about upcoming service requirements, ensuring timely maintenance without disrupting project schedules. Subsequently, this adherence to maintenance schedules minimizes costly downtime that could otherwise extend project timelines.
Quick-Service Access Points Design
The Grundodrill 5X features thoughtfully designed access points that simplify maintenance procedures. Its stainless steel construction offers improved contaminate control compared to other models, thereby reducing maintenance frequency.
The patent-pending onboard drill rod greaser represents a key maintenance-friendly feature. This system ensures proper lubrication of drill rods, which is crucial for achieving proper torque and preventing pipe unthreading or breakage downhole.
Primarily, the machine's design prioritizes accessibility, allowing technicians to quickly address service needs without extensive disassembly. This approach mirrors best practices from other pneumatic tools, where regular cleaning and proper lubrication significantly extend equipment life.
Parts Availability for Grundodrill 5X For Sale Models
Naturally, even well-maintained equipment eventually requires replacement parts. For Grundodrill 5X owners, parts availability presents minimal concerns. The manufacturer's competent service staff offers rapid assistance to minimize downtime.
New Grundodrill 5X models typically include warranty coverage, with standard terms including 30-day return policies. Nevertheless, wise fleet managers ensure they maintain adequate parts inventory for routine maintenance items.
For contractors considering a Grundodrill 5X for sale, this robust support infrastructure provides confidence in long-term ownership. Beyond parts, the manufacturer offers comprehensive training for operators and construction professionals, ensuring crews can perform basic maintenance tasks correctly. Technical support teams provide soil-specific expertise to help operators adjust maintenance routines based on working conditions. Additional information about parts and support is available through https://www.directional-drilling-store.com/.
Conclusion
The Grundodrill 5X stands as a remarkable achievement in horizontal directional drilling technology. This compact powerhouse proves that size does not limit capability, delivering impressive results through its innovative features and intelligent design.
Field results demonstrate the machine's ability to slash project timelines by up to 52% compared to traditional methods. The combination of dual-speed drilling technology, 15-second rod loading cycles, and precision controls allows crews to complete complex installations in days rather than weeks.
The user-friendly interface and automated systems make the Grundodrill 5X accessible to operators while maintaining peak performance. Smart maintenance design and readily available parts support ensure consistent uptime, ultimately reducing project costs and improving contractor profitability.
Through this comprehensive analysis, we have seen how the Grundodrill 5X transforms challenging drilling projects into efficient operations. The machine's proven track record in utility installations, coupled with its operator-friendly design and robust support infrastructure, makes it a valuable addition to any contractor's fleet.
For detailed specifications and current availability of the Grundodrill 5X and other directional drilling equipment, visit https://www.directional-drilling-store.com/.
Show facts
Comments